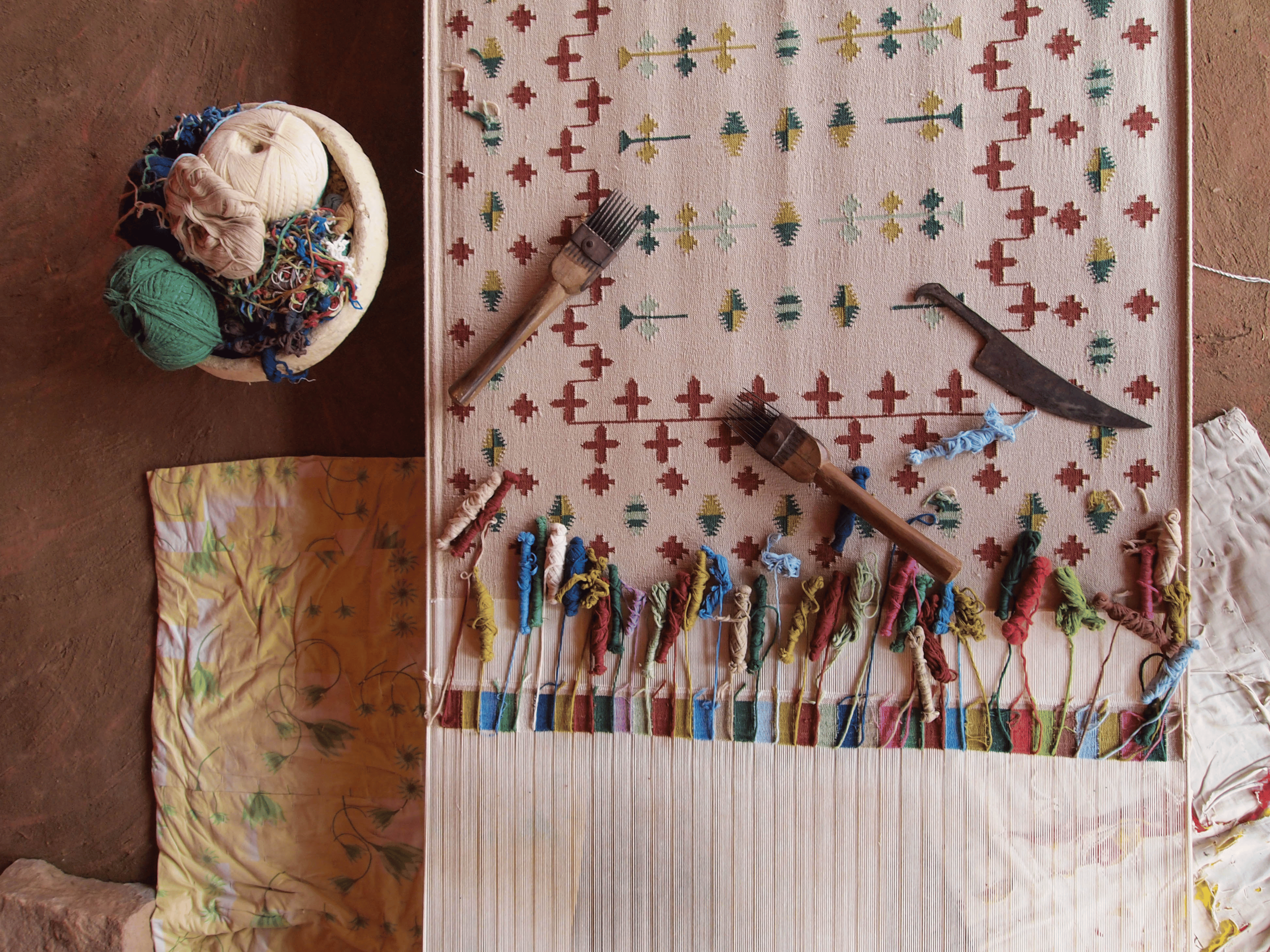
Rug Making Process
Transforming Designs into Masterpieces: The Art of Rug Making!
Before Weaving: A Journey of Craftsmanship
Each hand-crafted rug is a testament to artisanal skill, passing through the hands of 180 skilled artisans from start to finish. Every one of the 90 people involved possesses a unique, irreplaceable expertise, honed over years of dedication.
To bring together these diverse talents, we rely on a decentralized model, connecting step by step with specialists whose craftsmanship creates a level of quality that cannot be matched. This collaboration is made possible by bridges built on compassion, empathy, and love.
Sourcing Raw Materials: The Foundation of Handcrafting
True craftsmanship begins with the finest raw materials, each of which is carefully selected to uphold the artistry of the final product.
Wool We source Chokla wool, regarded as the finest Indian wool for rugs, from biannual auctions in Bikaner. This wool, sheared from sheep in the spring and fall, arrives in mixed textures and qualities, which are then meticulously hand-sorted by local artisans with irreplaceable expertise.
Merino Wool Imported from New Zealand, Merino wool is used in our premium 14/14 quality carpets and is also blended with other wools to create yarns of exceptional softness, durability, and sheen. We source wool from 18 different countries to create custom blends that unite lustre, texture, and resilience.
Silk For the finest quality silk, we look to both domestic traders and international sources, importing the best silk from China to complement our creations.
Carding & Spinning: A Heritage of Craft
Once the wool is hand-selected, sorted, and washed, it is passed to one of India’s rarest artisans: the Katwari, or spinner.
The Katwari begins with the process of carding, where wool is combed on bristled pads to remove dirt, knots, and clumps, ensuring uniformity and consistency. This labor-intensive process is followed by spinning the wool into yarn on a traditional charka (spinning wheel). The spinning process, steeped in India's heritage, transforms wool fibers into durable yarn with a textured pattern of thick and thin strands—much like the fabric of Indian history itself.
Today, more than 3,000 of these skilled artisans have found a home with us, preserving and advancing this ancient craft.
Dyeing: Art in Color
Dyeing is an art form that allows artisans to add vibrant decorative effects to the yarn. Before dyeing, the wool is segregated by color and texture. Lighter wools are reserved for paler dyes, while darker wools absorb richer hues. Blends of different wool types help to create yarns with the perfect balance of softness and resilience.
We use eco-friendly, GOTS-certified dyes from trusted sources like Colourtex and Hunstman, which ensure that the colors do not bleed or damage the yarn. Our custom recipes allow us to offer over 3,000 colors, with the ability to tailor hues to each project’s specific needs.
Once the yarn is prepared, artisans wind it onto frames and immerse it in boiling vats of dye. After soaking, the yarn is hung in the sun to dry before being stored for use. Each batch of yarn carries subtle color variations, a hallmark of handcrafted rugs known as Abrash or Antique, where these natural shifts give each rug a distinctive character that only time and traditional methods can achieve.
Weaving: The Craft of Precision
Weaving is the heart of rug-making, where skilled artisans meticulously transform yarn into intricate patterns and textures. Each rug’s character is defined by the weaving technique used, which directly impacts its design, quality, durability, and value.
Different weaving methods create distinct styles of rugs, from tightly woven, durable pieces to more textured, artistic designs. The precision and expertise of the weavers bring each design to life, knot by knot, row by row. Their hands work with remarkable accuracy, following centuries-old techniques that have been passed down through generations.
The choice of weaving technique is not only a reflection of artistic vision but also a measure of the rug’s longevity. Hand-knotted rugs, for example, are known for their exceptional durability, while hand-tufted and flat-woven rugs offer unique aesthetic qualities. The density of knots and the type of weave define the texture and intricacy of the design, ensuring that each rug is a masterpiece of both form and function.
At the core of the weaving process is a deep respect for tradition, combined with a passion for innovation. Whether creating a classic pattern or an entirely new design, the weaver’s skill is what ultimately transforms raw materials into a piece of art that will endure for generations.
The 18 Steps of Finishing a Carpet: Crafting Perfection
Completing a hand-crafted carpet involves 18 meticulous finishing steps, each contributing to the rug's final beauty and quality. When done entirely by hand, this process can take up to a month, perfecting the rug to a gleaming finish.
Measurement
Due to the natural variations in hand-knotting, carpets often differ slightly in length and width. Each rug is measured to ensure these variations stay within standard sizing limits, ensuring a precise fit.Knot Counting
To verify the integrity of the design, every knot is counted by hand. Line by line, the craftsman ensures that the exact number of knots matches the original design. If any knot is missing, it is identified and surgically repaired to restore the intended pattern.Pile Height Checking
The first quality check ensures yarn isn’t wasted and that the pile height meets quality standards. If the pile is too thick, the supervisor works with the weaver to adjust their technique, ensuring efficient yarn usage.Raffu – Repairing
If discrepancies in knot count or pile height occur, master artisans step in to repair them. Known as the “doctors of rugs,” these experts use large needles to seamlessly fix any issues. The precision is such that repairs leave no trace, restoring the rug to perfection.Thukai – Knot Beating
Due to the imperfections in hand-knotting, the design may warp slightly as the knots are uneven. Craftsmen use iron nails and hammers to gently beat the knots into alignment, straightening the design with precision and care.Kachi Kainchi – First Shear
The first round of shearing levels the pile height across the entire carpet. As the weaving process leads to minor variations in pile length, craftsmen use a shearing machine to even it out, preparing the rug for the next steps.Sua Birai – Design Correction
During weaving, yarns can intermingle and blur the design. Craftsmen use skewers to untangle and straighten the yarn, restoring the clarity and sharpness of the intended pattern.Back-burning
The back-burning process involves exposing the underside of the carpet to a flame or torch. This singes loose strands and tightens the knots, enhancing the rug’s durability by causing the yarn to shrink and strengthen.Back-burn Cleaning
After back-burning, the singed particles are brushed off, leaving the back of the rug clean and pristine.Dipping
The rug is submerged in a cleansing wash to remove impurities embedded in the fibers. The carpet soaks up the fluid, which then flushes out all unwanted particles, ensuring cleanliness.Washing
Washing a carpet is an art form in itself. Laid flat, the rug is bathed in water and a mild cleaning solution, with craftsmen using paddle-like tools to methodically wash and groom it. Each stroke flushes out dirt while strengthening the knots, in a process that is precise and efficient, lasting just 15 minutes.Khinchai – Stretching
After washing, the wool and underlying cotton warp and weft shrink slightly. To restore the rug to its original dimensions, it is stretched on an iron frame, ensuring the knots remain tight and balanced.Cutting
When the rug is taken off the loom, the edges are initially bound with warp and weft threads. This temporary binding is cut off to allow for more intricate and durable edge finishing.Binding
The edges of the rug are bound to ensure durability and add aesthetic appeal. While different patterns are used to style the width, the length is bound in a standard fashion for strength. Traditional rugs often feature tassels, while modern designs are fully bound on all sides.Pucci Kainchi – Final Shearing
In the final round of shearing, the desired pile height is precisely set. This measured height determines the rug’s category before it is ready for sale.Kalam Birai – Detailing
Artisans use needles to meticulously refine the design, separating each interlocked yarn knot by knot. This step sharpens the pattern, giving the rug its final, perfected look. “Kalam Birai” translates to “correcting by pen,” a fitting description for this intricate process.Chinte Nikalna – Snipping Visible Cotton
In this step, artisans comb through the rug to find and snip any visible cotton threads, ensuring a flawless finish. Though simple on cloth, this task is far more challenging on a rug, requiring great attention to detail.Carving & Embossing
Khadi Gultarash (Carving) is used to create sharp, defined cuts in the design. The artisans keep scissors straight and cut along the lines to enhance the rug’s pattern.
Put Gultarash (Embossing) creates a high-low effect in the rug by cutting with scissors held at an angle, giving the design a three-dimensional texture.
Each step in this intricate process contributes to crafting a rug that is not only visually stunning but durable enough to last for generations.